We have all seen them. We have picked up a perishable product and seen either a series of numbers or combinations of letters and numbers sitting on a label. Usually, it is right next to the expiry date. What is this mysterious code? What does it mean, why is it there, what purpose does it serve?
That mysterious code is called a lot number. As a herbalist you may know it as a batch number. They are the same thing. It is a unique number or combination of letters and numbers that identifies a particular product, made on a particular day, with particular ingredients in a manufacturer’s inventory.
The purpose of the lot number is to allow the manufacturer of the product to identify the time, place, ingredients and process used to produce the product. If the product produced doesn’t meet the quality standards of the manufacturer, they can use the lot number to determine what went wrong in the manufacturing process. This allows them to improve their processes so they produce more consistent and higher quality products.
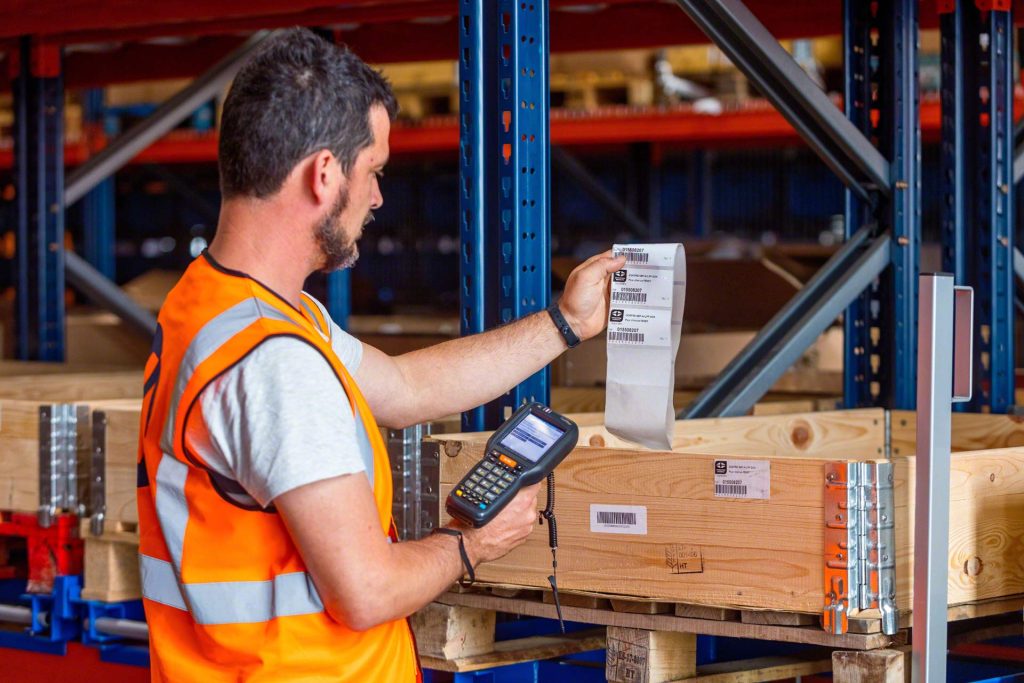
In addition, if a defective product gets sold to a customer or distributor, the lot number gives the purchaser of the product a way to communicate to the manufacturer exactly which products they are. The manufacturer can then use the lot number to determine who else they sold the defective product to so they can be notified. This notification is commonly referred to as a recall. A manufacturer recalls a product when it is defective and the use of it can cause bodily harm, illness or death.
This is especially important when you are making products that people consume or put on their skin. If an ingredient is tainted or it was processed incorrectly, people can get ill. This is where lot numbers become really important. So much so that many jurisdictions require consumable and topical products to have them by law.
As important as lot numbers are, there is no standard format for them. You can use just letters, you can use just numbers or a combination of both. The important thing is no two products that you make can have the same one. Each time you make the product, you have to give it a new lot number.
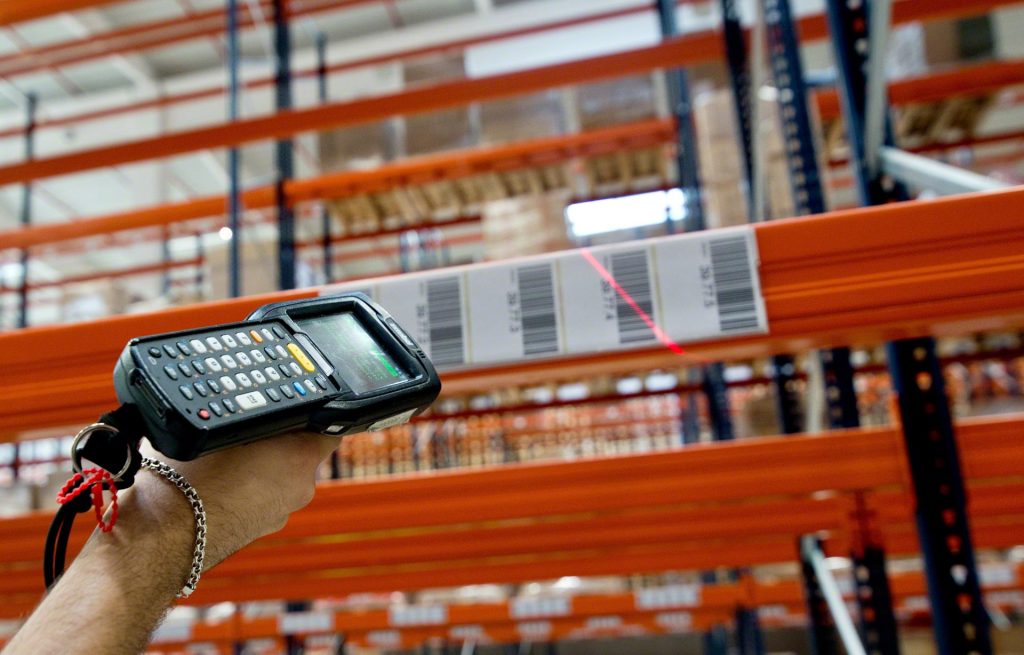
If you make calming tea on Thursday at noon and give it one lot number, when you make the same calming tea two hours later, you have to give it a different one. Even though you are making the exact same product, there can be variations in ingredients, how they are measured, the cleanliness of the equipment etc., etc. All of this needs to be accounted for. Having unique lot numbers ensures that happens.
Lot numbers can be a completely random jumble of characters or they can have a specific format. If you are doing all of your paperwork manually, it is easiest to consistently generate unique lot numbers using a specific format.
For example, a herbalist might want to use the format 05122022FRSM1, which is the month, day and year the product is made, the first two letters of the first name of the person who made it, the first two letters of the last name of the person who made it and the number of the product made that day. The downside to this method is you have to keep track of how many products the person made that day to make sure no lot numbers are used more than once.
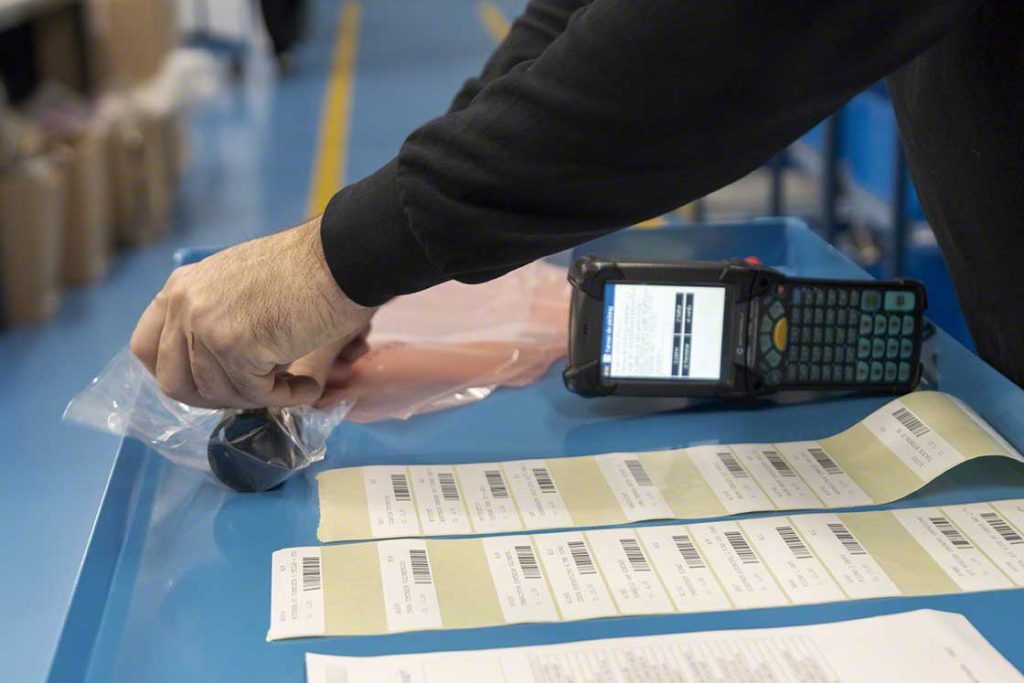
If you are using software like Kerrii, to do your paperwork then it is easiest to let it generate random unique lot numbers for you. In fact, it is so easy that even those herbalists who are determined to use a specific format to generate their lot numbers soon give up when they realize how much time they save letting the software do it.
As useful as lot numbers are for tracking what product was produced when and who it was sold to, they alone will not help you determine what went wrong when you produce a defective product. To truly be useful, the lot numbers of all the ingredients, the process used to manufacture the product and the conditions under which it was manufactured should all be recorded along with the product’s lot number. Without this information, you will know that a product is defective but you won’t know why.
There are many ways you can record this information. You can use a spreadsheet or create a form. The form can be printed out and filled out using a pen or you can fill in the form electronically. At a minimum, you should record all the ingredients used and their lot numbers, the name of the product you created and the lot number of the product itself. Every time you make the product, you fill in a new form or spreadsheet.
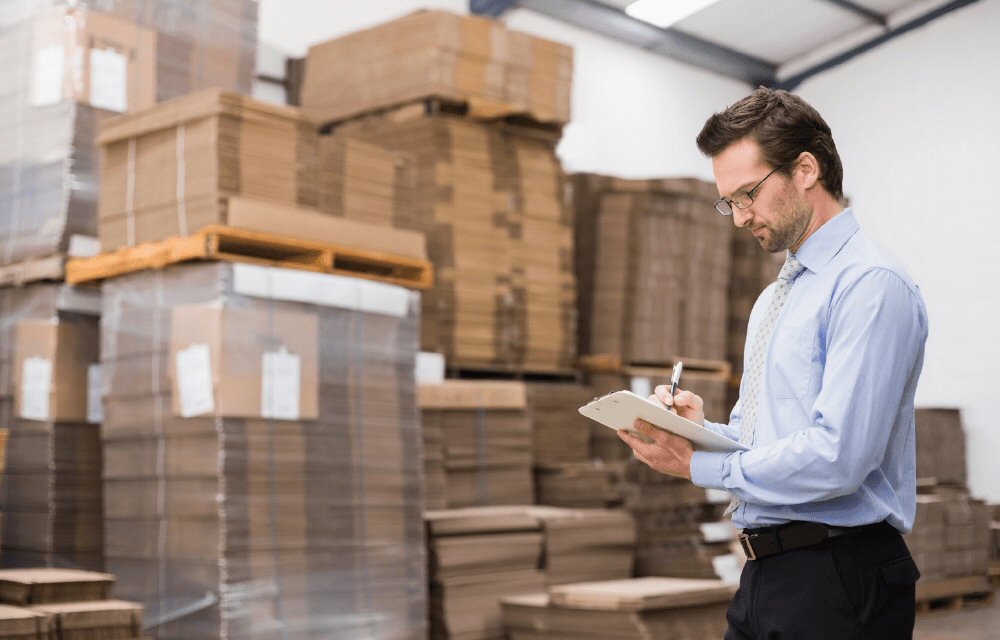
You can also include the instructions for making the product and the equipment used as well as other information in your spreadsheet or form. However, it can get rather tedious entering that information every time you make the product. If you use the same process to produce the product every time, you can streamline things by storing that information on a separate generic recipe sheet and only referring to it should you need to investigate the reason the product is defective. If, however, you change something about the process, you need to record those changes on the spreadsheet or form for that batch.
There is software like Kerrii, which can do the record keeping for you. The advantage to using software is that it allows you to easily search for a particular lot number and find what product was used where.
This saves you a lot of time as you don’t have to manually search through forms or spreadsheets to find which products need to be recalled. In addition, it can store your recipes and keep track of your ingredients.
Regardless of which record method you use, using lot numbers will ensure you maintain the quality of your product and are able to notify your customers should something go wrong.
Article written by Bernadette Ann.